4 Key Components of a High-Quality Band Saw Blade
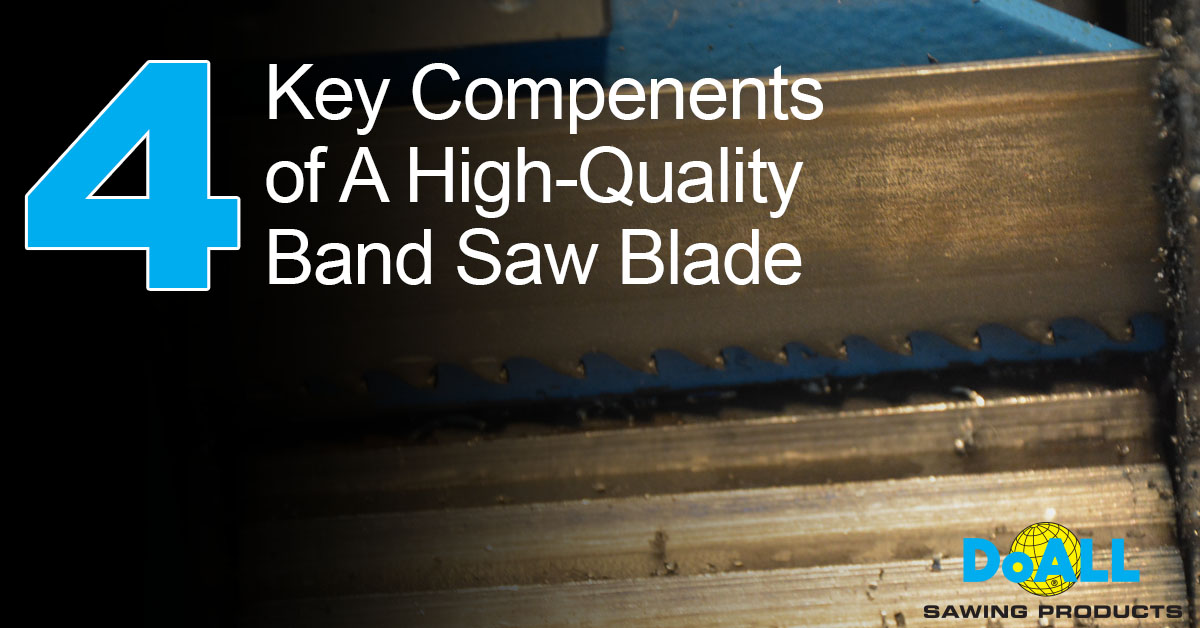
Do you want to improve accuracy, save time, and money in your metal cutting process?
Choosing the right band saw blade is crucial for achieving increased efficiency, and cost savings. With so many options available, it can be overwhelming to determine which blade is best suited for your specific needs. But don’t worry! By understanding the 4 key components of a band saw blade you'll be equipped to make an informed decision and select the perfect blade. In this post, we'll discover the four keys to achieving accurate parts and optimal performance with your sawing equipment. So, keep reading for some pointers from DoALL Sawing Products.
Key Components of a Band Saw Blade
Are you wondering what separates an average band saw blade from a truly exceptional one? Well, the secret lies in its key components. Let's take a closer look, shall we? The teeth, gullets, blade width, and tooth material considerations all play a crucial role in the blade's performance. First up, we have blade teeth and shapes. The blade teeth and shapes are the ones responsible for making those precision cuts in your material. But what about all the chips that come with it? That's where the gullets come in, to transport chips away from the cut channel. Finally, we have the body of the blade, providing stability and support throughout the cutting process. Without these components working together, you might as well be cutting with a butter knife.
Key Component #1- Blade Tooth Shapes
One critical factor behind achieving precision cuts made by a band saw blade lies in the shape of the tooth. Tooth shapes are a combination of rake angles and gullet shape. Two common tooth types are precision or claw/hook. The rake angle is a measure of the tooth face inclination to the work and can be negative, neutral, or positive. The precision-shaped tooth is a generalist shape and can be used for most sawing applications, while the slightly more aggressive claw/hook-shaped tooth is often used when increased cutting rates are desired. Negative rake-angled blades are excellent when cutting hardened materials. Neutral rake-angled blades are often generalists as well and will be used in several material types from mild steel to exotic alloys. Positive rake-angled blades are used when a more aggressive cutting action is needed from softer non-ferrous materials all the way to titanium. Understanding the different tooth shapes and rake angles can help you achieve the perfect cut for your specific cutting needs.
Key Component #2- Blade Gullets
Have you ever wondered why a band saw blade has those U-shaped spaces between the teeth? They're called gullets, and they play a crucial role in keeping your cutting channel clean. You see, as the blade cuts through the metal, chips can start to accumulate. The chips, if not removed from the cut channel, will clog the blade. This greatly reduces the useful life of the tool. If the gullets are clogged, they will not carry the chips. This results in an increased load on the blade and the machine. It can contribute to the hardening of the material, blade bounce, stripping of teeth, and chips being welded to the blade. That’s where the gullets come in - they create space for the chips to be carried away from the cut preventing them from building up. Combined with the proper coolant choice (we’ll talk about Coolants in another article!) the saw blade gullet is an important aspect to the sawing process. So, the next time you're using a band saw blade, remember to appreciate those little U-shaped spaces that keep your sawing operation running smoothly!
Key Component #3- Blade Width
The width of a band saw blade also plays a significant role in its performance. Thicker blades provide more stability, known as beam strength and can handle larger dimensions and tougher materials, while thinner blades are better for intricate radius cuts. The narrower the blade, the tighter the radius that can be cut. It is important to consider blade width based on the type of band saw machine, the material being cut, and specific application.
Key Component #4- Blade Tooth Material Considerations
Band saw blade teeth come in a variety of materials. The three most common are carbon steel, bi-metal, and carbide. Each material has its unique benefits and drawbacks. Carbon tooth steel blades are an affordable general-purpose option but may not last as long as the other choices. Bi-metal tooth blades are by far the most often used in metal cutting applications and offer a decent lifespan cutting a wide variety of materials from mild steel to tool steel. Carbide tooth blades are made from a harder material than bi-metal blades and can handle the most demanding cutting applications. When deciding on a tooth tip material for your band saw blade, consult a professional to discuss the material being cut, the size of the material, and desired production volume. Then, you can estimate the cost per cut and determine the most cost-effective band saw blade tool for you and your operation.
In conclusion, finding the right band saw blade for your metal cutting needs may seem daunting, but by understanding the key components, tooth shape, gullet configuration, blade width, and tooth material composition, you can make an informed decision. Remember, a high-quality band saw blade can make all the difference in achieving repeatable accuracy and profitability. Consult with your DoALL band sawing subject matter expert when considering your specific cutting needs and choose a band saw blade that will help you achieve the results you're looking for.
Discover the Trusted Industry Leader for Metal Cutting Blades and Band Saw Machines
When it comes to metal cutting, DoALL is the trusted industry leader renowned for its quality and exceptional customer service. With an extensive range of band saw blades and band saw machines, within our product line-up, you will find the perfect solution for your operation’s needs. Our team of sawing subject matter experts is always on hand to offer support and advice to help you maximize the benefits of your equipment. Want to learn more about our top-notch products and services? Visit our website and take the next step in metal cutting with DoALL.